How is polystyrene production done? As you know, polystyrene is known as the sixth most widely used styrene in the world. This material is known as a type of synthetic aromatic polymer that is produced by a styrene monomer. The polystyrene production process, which is a type of thermoplastic material, is performed using processes such as extrusion in both solid and foam. In the end, this material can become the final product.
Typically, polystyrenes are used to process plastics. The major method of polystyrene production is ethyl gasoline. Ethyl is first alkylated with ethylene and then dehydrogenated, which is carried out using a catalyst for aluminum-silica, solid phosphoric acid-styrene to styrene.
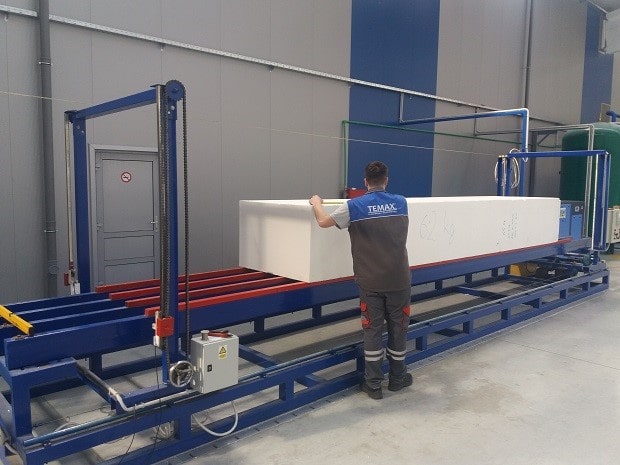
Polystyrene production
How is polystyrene production done?
To produce polystyrene, benzene is first combined with ethylene to obtain ethylbenzene. The important point here is the formation of styrene from the dehydrogenation of ethylbenzene.
Oxygen is required to produce styrene. It is also necessary to have access to factors such as light or oxidation as a catalyst. By performing this operation based on the polymerization process, free radicals are polymerized and thus polystyrene is made.
Regarding the structure of polystyrenes, we must say that this material belongs to the vinyl family, which has a long chain of hydrocarbons that are connected to a group of phenyls one by one to each carbon atom.
Polystyrene production through suspension polymerization
In this polystyrene production method, a catalyst is monomerized and then dispersed in water. A separate suspending agent is added to the suspension to stabilize the process.
Commonly used agents in suspension or suspension include a variety of pectins with cellulose, as well as gelatin, polyacrylic acid, and polyvinyl alcohol.
In some cases, inorganic agents are used for suspension. These materials include magnesium silicate with a variety of phosphates as well as kaolin and other materials such as zinc oxide and aluminum hydroxide.
Suspension polymerization is usually considered as art until the science of this process leads to controlling the size and distribution of the polymer. The shear distribution in the reactor is directly related to the design of the reactor and the agitator, this can have a huge impact on the particle sizes of the polystyrene in this method.
Another factor influencing the size and distribution of polymers is the suitability of the monomer with solvent or water, as well as the reaction to heat and the type of primers and their consumption and suspending agents.
The polymer is produced by larger polystyrene particles in the form of a single split, which is performed by a special fan. This includes the suspension polymerization of the grain. Another case recorded for the suspension polymerization of styrene is the use of ultrasound.

Production of polystyrene with suspension polymerization
Polystyrene production by massification process
The mass polymerization is done by heating the solvent-free monomer with primers, often benzoyl peroxide, in a container.
This method has the disadvantage of separating the polymer from the reactor or balloon and extracting and dissipating the heat generated by the polymer.
Forming process in the production of polystyrene
This process on polystyrenes is often done by injection. But due to the high processability of this material, it responds in other ways. Several types of polystyrene are highly resistant to a wide range of chemicals, including weak acids, salts, alcohols, and bases.
These polystyrenes are made according to the FDA standard used in the food industry. The production process of this type of polystyrene is in two stages. First, it is placed at a temperature of 80 degrees Celsius and then placed at a temperature of 100 to 180 degrees Celsius.
Currently, about 12% of the soft plastics market belongs to polystyrene. These materials can be softened at 90 ° C and require a temperature of 180 to 250 ° C for melting and molding.