Expanded polystyrene (EPS), also known as ionolite or plastofoam, is a white, lightweight, soundproofing, and moisture-insulating material first used by the Germans in World War II to build bridges. Floating was produced on the water. Expanded polystyrene (EPS) has several applications in packaging and insulation. This product is the most suitable option as an alternative to cement blocks for sound, heat, and cryogenic insulation, and also has many applications in the manufacture of packaging foams and food storage containers. In this article, we will learn more about the forming process and the method of producing expanded polystyrene (EPS) and its features.
Introduction of Expanded Polystyrene (EPS)
Expanded polystyrene, also known as EPS and ionolite and plastofoam for short, is a white, fire-retardant polymer made by combining polystyrene with a foaming agent. Polystyrene belongs to the family of thermoplastics and has a linear chain.
Expanded polystyrene (EPS) is formed by the dehydrogenation of alkylbenzene polystyrene monomers. Due to the release of gas inside this material, the volume of polystyrene grains increases by forty times their original size. After the expansion operation, the expanded grains are molded according to the type of application.
Features of expanded polystyrene (EPS) materials include low thermal conductivity, acoustics and refrigeration, low weight, high impact resistance, fire resistance and fire, and having suitable mechanical properties such as pressure resistance.
In addition, very low heat transfer, low moisture absorption, excellent dimensional stability, insensitivity to water, ability to prevent energy loss, chemical neutrality, and resistance to bacterial attacks.
Investigating the process of producing expanded polystyrene foam (EPS)
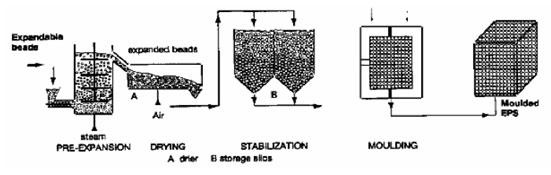
EPS Forming
The initial foaming process:
Initially, the foam formulation components need to be mixed. Shortly after the onset of chemical reactions, the color of the system becomes cloudy and gas bubbles (which are also visible to the naked eye) form. This short time interval from the beginning of mixing to the observation of the cream color in the reaction system is called the creaming time.
As mentioned, due to the short time, the viscosity of the mixed fluids is high and the flow of materials in the mold is poor. Therefore, to produce a uniform foam, the casting process must be performed continuously and uniformly inside the mold. Then, when the gases produced in the liquid system are well dissolved and saturated, the primary nuclei are formed.
Now, the foam is formed, it moves upwards. Simultaneously with the process of production and continuous formation of gas, the produced gas molecules are transferred from the liquid part into the formed cells and nuclei. It should be noted that the smaller the size of these nuclei (cells), the greater the pressure inside them. This causes the smaller cells to become unstable and to merge into adjacent cells larger than themselves. After a while, the total number of cells will decrease and their size and volume will increase.
Also, these cells are spherical at the beginning of formation, but over time, they stretch in the direction of rising foam and become polygonal. The shape of these cells is based on creating the minimum surface area and having the least possible energy.
The process of producing expanded polystyrene foam (EPS) consists of three steps, each of which will be described separately below.
Pre-expansion:
To mold the parts, in the first stage, which is called pre-expansion, it is necessary to prepare the raw puffed material with the necessary density. Polystyrene beads (containing puff-forming agent) prepared during the initial foaming process are fed into a vertical tank equipped with a stirrer.
The tank also has steam, air, and an automatic system for forming expanded grains also called puffs.
By controlling and adjusting the speed of the stirrer as well as the feed rate to the tank (including such as airflow, raw materials, and streamflow), polystyrene granules soften above the boiling point of the blowing agent at about 90 ° C.
The amount of vapor pressure inside these grains also increases. In general, performing this stage of the process will cause the grain to expand and increase in volume and reach the required density.
The minimum density obtained depends on factors such as crop type, initial grain size, puffiness, and the use or non-use of additives. The volume of these grains is increased up to 40 times before the pre-expansion process.
At the end of this stage, these seeds are kept in open containers for some time (up to several hours). This action causes the vacuum created inside these grains to balance with atmospheric pressure in addition to the release of the puffing agent.
After the pressure stabilization step, the initial puffed grains are poured into a closed mold and subjected to steam heating again. At this stage, the primary puffed grains penetrate each other to form a monolithic mold.
If the pre-expansion stage is performed in a discontinuous manner, the polystyrene beads must be pre-weighed and continuously inserted from the end of the pre-expansion tank.
Expanded and puffy seeds should also come out of the upper part. Adjusting and controlling the density of the final products is possible by controlling the pressure and temperature of the pre-expansion tank and the duration of the presence of the grains in the expander.
Finally, the products removed from the pre-expansion tank are transferred to a fluidized bed dryer and then dried.
Initial puff stabilization:
At this stage of producing expanded polystyrene, the raw product removed from the fluidized bed dryer enters large containers to reach normal temperature (close to ambient temperature).
At the same time, which may take three to four days, depending on room temperature, airflow, and density, water vapor around the grains and the residual puffy agent condenses. Also in this process, air can penetrate the grains.
Molding:
At this stage of producing expanded polystyrene, the structure and shape of the molds are determined depending on the type of foam produced and its application. The molds can be made of aluminum, galvanized or ordinary steel, or even wood. If the same mold is used, more materials are used in closed molding processes than in open molding.
Also, the density of the foam increases, and a lot of pressure is created in the mold. Blockchains have six walls that are in contact with the expanding grains. These walls must be covered with Teflon or steel and have a large number of small holes less than one millimeter in diameter to allow steam to enter and air to escape from the mold.
There are three main types of open molds, include complex molds, vacuum molds, and transition molds.
Shaping foams:
This is the final step in producing expanded polystyrene foam (EPS). In addition to the molding process, foams can be transformed into various shapes as desired by combining pressure and cutting. Foam edges can also be formed using the polishing process.