Selecting polymer to produce polymer products
By choosing the right polymer to produce polymer products, good progress can be made. If the right polymer is not selected, the polymer products will not be substandard. The more suitable polymer you choose, the better polymer products with better quality properties and properties are produced.
If polymer products are used outdoors, the polymer must be suitable for UV protection. To produce polymer products, it is necessary to be aware of the specifications and properties of plastic raw materials to produce suitable polymer products.
Different properties of plastic materials
Some plastics are sticky and others are highly tensile. Paying attention to the temperature characteristics of plastic materials also plays an important role in the production of polymer products. Unlike metals and ceramics, these materials have strain and pressure properties. Plastics are flexible compared to many other materials.
Any incorrect choice of polymer can lead to the production of hazardous plastics. Understanding all the properties and characteristics of suitable polymeric materials will lead to the production of quality plastic products.
Choosing the right polymer will result in the production of high-quality polymer products. The better the quality of the polymer, the more quality polymer products can be produced.
Production cost is another factor in production, but sometimes you do not need to use expensive polymers. Inexpensive polymers often cannot solve the problem.
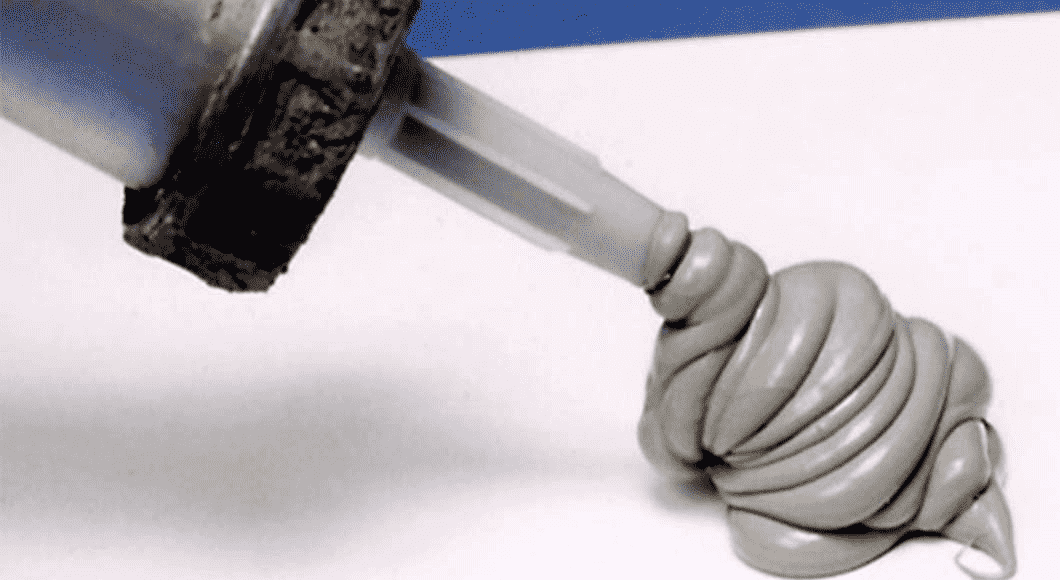
Properties of plastic materials
Silicon
Silicon is the most common material used in the production of polymer products. Silicon is used in many polymer products.
The most important properties of silicone
- Resistance to very high and low temperatures between – 65 to 260 degrees Celsius
- Resistance to ultraviolet rays
- Resistance to ozone
- Resistance to mechanical wear
- Resistance to abrasion and compression
The cost of producing silicon is very high, but it has excellent features that many manufacturers can use to produce high-quality polymer products.
Styrene-butadiene rubber (SBR)
The cost of preparing this material is less than silicon, and many manufacturers can produce excellent products by providing this suitable polymer.
The most important properties of styrene-butadiene rubber
- Resistance to very high and low temperatures between -65 to 180 degrees Celsius
- Abrasion resistance
- Adhesion to hard and solid metals
- Impact resistance
It costs very little to prepare and is much less resistant to chemicals, and you can get it at the lowest cost.
Fluoro-silicon
This material is very expensive and very resistant to other chemicals. Fuel chemicals such as gasoline and oil do not affect them. This material is used in aerospace applications and industrial lubricants.
The most important properties of fluoro-silicon
- Resistance to very high and low temperatures between -29 to 176 degrees Celsius
- Resistance to industrial oils and solvents
- Resistance to a variety of liquid fuels, gasoline, and oil
- Resistance to air, ozone, sunlight
- Aromatic
- Chlorine
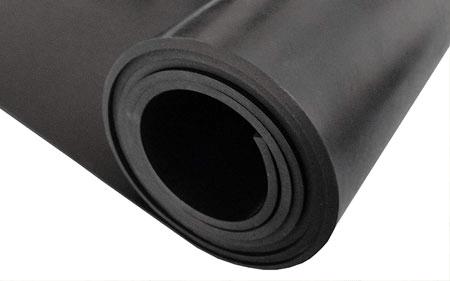
Choosing the right polymer
Selecting the right polymer for the production of plastic products
A suitable polymer is required to have all the mechanical and chemical, electrical, thermal properties to be able to produce durable plastic products that include many applications. It is better to be able to produce plastic materials and products by recycling its waste materials.
High Impact polystyrene
High Impact polystyrene is used in the manufacture of computer, telephone, and television enclosures. Of course, this material is also used in making refrigerators. Production of various toys Other uses of this material.
Buy Phthalic Anhydride (PA)
Phthalic anhydride (PA) is one of the most suitable polymeric materials for the production of polymer products, which can also be used to produce plastic resins. This material can be used in the production of dyes, pharmaceuticals, and the textile industry. You can buy this material from Moheb Baspar Company.
Buy Dioctyl Phthalate (DOP)
Dioctyl phthalate (DOP) is very resistant to light, air, water and is used in the production of wires and cables. It is the best electrical insulation and Moheb Baspar Company produces this material and offers it at a reasonable price.
General Purpose Polystyrene (GPPS)
General Purpose Polystyrene (GPPS) is a transparent polystyrene-based chemical that can be produced by injection and extrusion. It is very resistant to heat and freezing. You can buy this material at a reasonable price from Moheb Baspar Company.
Conclusion
Choosing the right polymer to produce polymer products is very important in the chemical industry. Products such as resin, silicone, styrene-butadiene rubber, fluoro silicone are among the best polymeric materials suitable for the production of plastic products.
Each of these polymeric materials is resistant to very high and low temperatures, abrasion, industrial oils and solvents, and liquid fuels. In addition, they are resistant to air oxidation, UV, each of which is a great advantage.