The most important physical and mechanical properties of high impact polystyrene (HIPS)
What do you know about the properties of high impact polystyrene ? High Impact Polystyrene, abbreviated as HIPS, is a type of impact-resistant plastic used in the manufacture of home appliances and utensils. It is very suitable for wet places due to its durability. This plastic is available in the market in terms of weight, flexibility, lightness, and reasonable price, and due to its extraordinary properties, this product is used in most industries.
High Impact Polystyrene, commonly known as HIPS, is a generic version of polystyrene rubber. The addition of rubber makes the thermoplastic extremely durable and has a much higher strength than its previous composition. Like all thermoplastics, it becomes soft and pliable when heated and solidifies again when cooled. These factors alone make HIPS an excellent material for parts production.
HIPS has various properties that allow a wide range of thermoplastic applications. With more rubber content, this material can easily go through production processes such as vacuum formation and can easily bend and mold while maintaining its durability.
After re-molding, its properties do not weaken. As a result, it becomes a widely used product. Due to its amorphous properties, HIPS can be painted, so it is great for design purposes that require beautiful beauty.
Due to its wide thermoplastic properties, there are many different applications of high-impact polystyrene (HIPS). Thermoplastic is ideal for marketing purposes due to its strength and durability and is often used for sales displays and advertising signs. It can also be used for thermoforming chambers and car parts, modeling, and plastic toys. In addition, thermoplastics are commonly used to make cabinets and shower enclosures.
High impact polystyrene has great features:
- Good molding
- High strength
- Re-processing
- Maintain dimensions and temperature
- Adhesion
- Printability
- Paintability
- Flexibility
Applications of HIPS sheets according to properties of high impact polystyrene
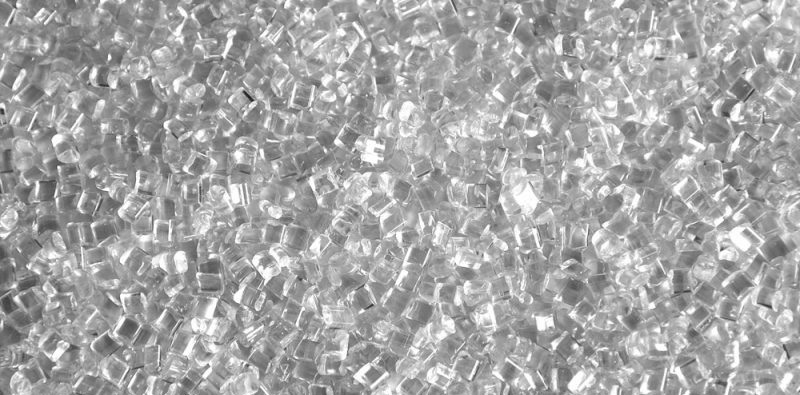
HIPS
It can be used in various industries due to its reasonable price and availability. They are used as heat and sound insulation. Among the uses and applications of HIPS, we can mention items such as the production of toys, sports equipment, home appliances, refrigeration insulation in the body of refrigerators and freezers, the manufacture of stencils, sanitary ware, disposable containers, and billboards.
HIPS sheets are one of the 5 basic resins used in electrical applications and construction compounds according to the mentioned characteristics.
These sheets have the following physical and mechanical properties:
Parameter | Amount | Standard | Unit |
Tensile strength | 300 | ASTM D 638 | Kg / cm2 |
Elongation Percentage | 65 | ASTM D 638 | % |
Flexural Resistance | 350 | ASTM D 790 | Kg / cm2 |
Flexural modulus | 17500 | ASTM D 790 | Kg / cm2 |
Hardness | 64 | ASTM D 785 | L Scale |
Impact strength | 10 | ASTM D 256 | Kg.cm/cm |
Thermal softening point | 97 | ASTM D 1525 | ºC |
Thermal deformation temperature | 78 | ASTM D 648 | ºC |
Water absorption | 0.05 | ASTM D 570 | – |
According to the above table, the amount of tensile strength is measured by ASTM D638 standard and according to it, its value is 300 (kg / cm2).
Also, Flexural modulus, which is important for us in this table, is obtained from the ASTM D790 standard, which has a value of 17,500 (kg / cm2).
Other properties of high impact polystyrene are also obtained according to the relevant standards and are collected in the table above.